ABOUT
For plano parts, surface flatness is defined to be the amount by which the actual part differs from a perfect plane. For radiused parts, two numbers are typically used to specify surface shape. Power is how closely the average part radius matches the specified value, and irregularity is how far the part departs from its ideal shape (e.g. a perfect sphere or cylinder).
Recent Posts
- Angle of Incidence
- Diameter Tolerances
- Extinction Ratio
- Reflectivity
- Surface Quality
- Material
- Surface Roughness
- Infrared Optics
- Dimensional Tolerances
Flatness and power
Flatness and power/irregularity are typically measured using an interferometer. These instruments use a laser to illuminate the test surface and produce a pattern of interference fringes (light and dark bands) which constitute a “topographical map” of the surface. The spacing between adjacent fringes corresponds to a vertical displacement on the part surface which is half the wavelength of the light which is being used for illumination (λ/2). As a result, surface flatness is generally specified in units of wavelength (such as λ/10, or tenth wave) rather than as an absolute number, along with the illuminating wavelength.
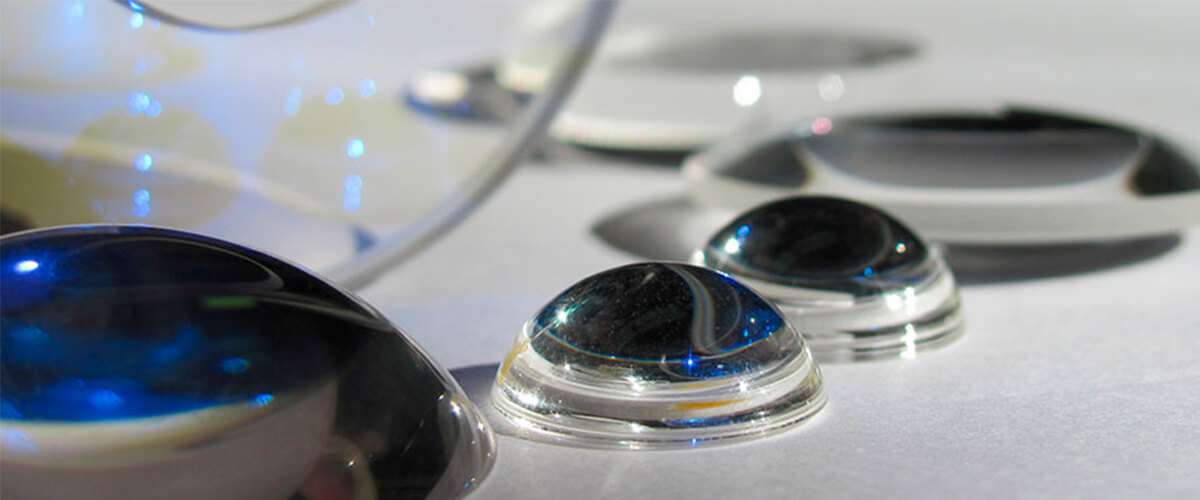
ARO employs Zygo interferometers in both our optical fabrication and Quality Control departments for flatness and power/irregularity measurements. Our Fabrication interferometers are set up to measure parts when they are still attached to the polishing block, which enables us to obtain rapid feedback on the status of the process.
Fabrication of high performance optical components requires maintaining a delicate balance between various parameters, such as surface flatness, surface quality and surface roughness. For example, longer polishing times generally produce better surface quality, but make it more difficult to hold a given surface figure. To consistently obtain the required results in a cost effective manner ARO utilizes a variety of different polishing techniques and fabrication equipment, depending upon part shape, size, substrate material.
Coatings
It should also be noted that most thin film coatings are deposited at high temperature, and mechanical stress is introduced into a coating when the part subsequently cools. Depending upon part size and shape, this can distort the optic and change its flatness. For demanding custom applications, ARO has a number of techniques to counteract this effect and deliver optics with high post-coating flatness. For example, pre-figuring involves purposefully polishing a slight curvature on a substrate with the intention of having the coating stress distort the optic back into flatness. Another technique, useful for first surface reflectors, is backside coating. Specifically, a single layer coating is placed on the second surface of the optic to balance and null out the overall mechanical stress on the part. ARO has also developed expertise in the production of multilayer thin film coatings that use a combination of coating materials with both tensive and compressive characteristics in order to minimize overall stress. Typically, coating stress is highly dependent upon ambient temperature and humidity, so development of high post-coat flatness optics requires an understanding of exact use conditions, and close cooperation between ARO and our customer.