Recent Posts
- Angle of Incidence
- Diameter Tolerances
- Extinction Ratio
- Reflectivity
- Material
- Surface Flatness
- Surface Roughness
- Infrared Optics
- Dimensional Tolerances
- Optical Resources
scratch and dig (SAD)
Surface quality, or scratch and dig (SAD), relates to the number and apparent size of visible defects, typically scratches and pits (called digs), on the part surface. While this may seem straightforward, probably no optical specification causes greater confusion. The problem arises because the assessment of scratches and digs is performed using a purely visual, non-quantitative comparison to a set of standards which conform to the military specification MIL-O-13830. This situation arose because the specification was developed many years before the advent of the laser, when surface quality was primarily a cosmetic, as opposed to a performance, consideration. Scratch-dig is specified by two numbers, such as 40-20. The first relates to the apparent size of scratches, and the second to the apparent size of digs. ARO performs SAD visual inspection in conformance with MIL-O-13830, utilizing a traceable set of standards.
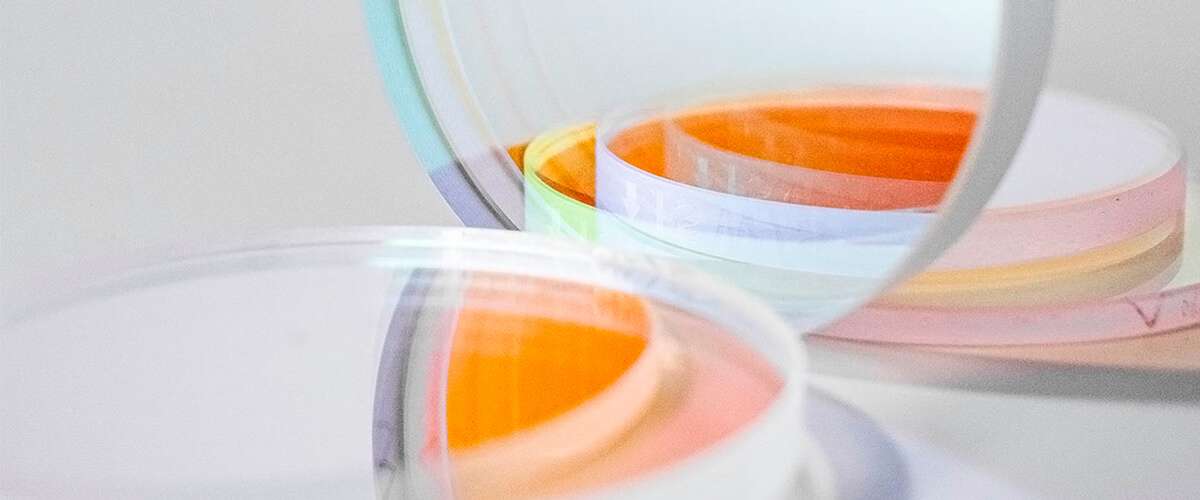
Fabrication of high performance optical components requires maintaining a delicate balance between various parameters, such as surface flatness, surface quality and surface roughness. For example, longer polishing times generally produce better surface quality, but make it more difficult to hold a given surface figure. To consistently obtain the required results in a cost effective manner ARO utilizes a variety of different polishing techniques and fabrication equipment, depending upon part shape, size, substrate material.